Air sealing is generally considered one of the most cost-effective ways to reduce energy use in buildings. That’s why advanced air sealing is an essential element of zero energy homes. As ever more sophisticated means of plugging leaks have been applied, the air leakage rates of new homes have slowly, but consistently declined. A decade ago, a typical mass-produced home might have an air leakage rate of 8 to 10 air changes per hour at 50 Pascals (ACH50). Today, the leakage of a typical new home may be down to 4 or 5 ACH50. Most zero energy homes push the leakage rate to 1.0 or 2.0, while Passive House requirements allow a maximum leakage of 0.6 ACH50.
A builder once called tracking down air leaks “death by a thousand cuts.” Large gaps, such as that huge hole in the floor sheathing that plumbers cut below the tub, are easy to see and address. But, it’s the tiny cracks and gaps—some too small to see—that increase cost and tax patience. The process has been somewhat subjective and uncertain. Even after hours of work it can be difficult to determine the actual air leakage rate until the building is tested.
A Game Changer?
There’s a new approach that may change the nature of the air sealing process and transform it from an art to a science. Aerobarrier is an aerosol sealant that fills all gaps less than ½-inch in just a few hours. The process uses a blower door to pressurize the building and automated sprayers to create a fog of acrylic sealant inside the building. As this fog travels along the air leakage pathways, it passes through the gaps in the building envelope, where it accumulates on the edges of the openings. After a few hours, the sealant fills all the gaps. Best of all, you can dial in a specific level of air tightness to meet a specific energy performance goal.
How it Works
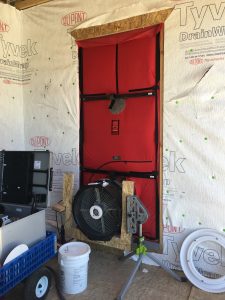
A blower door is used to pressure the building, forcing Aerobarrier sealant into gaps and openings.
Preparation includes what you might call gross or large scale air sealing. This includes blocking that hole under the tub, covering open wall cavities behind fireplaces, all the typical fire caulking around pipes and wires, etc. But any remaining gaps less than ½-inch can be skipped.
Then, the construction sequence must progress to a stage where the building can be pressurized. The easiest stage in a normal construction schedule would be after drywall has been installed. While the sealant will not accumulate on vertical surfaces, it’s still necessary to cover windows, exhaust fans, and duct registers.
Equipment setup involves mixing the acrylic sealant and setting up the pump and blower door for building pressurization. Several aerosol spray heads are placed around the building. The blower door runs to maintain the building at 100 Pascals of positive pressure while the sealant is sprayed into the air. Most homes require three to four hours to reach the targeted level of tightness. Tighter results require more time. A computer controls the process and monitors air leakage, so the operator can stop when the desired level of air leakage is reached.
Because the official building air leakage is measured using building depressurization, the blower door fan must be reversed to document the final air leakage rate.
The cured sealant does not emit volatile organic compounds into the finished home. However, it’s hazardous to enter the building during the operation without a full face respirator and outside air supply due to the danger of breathing aerosols. The sealant is Greenguard Gold certified for low toxicity. The sealant is ultra-low VOC with no off-gassing and it has no Red List items, so it is safe to use inside the house.
Cost
Aerobarrier is licensed to local operators, who set their own prices. Two factors affect the total cost: level of air tightness and building size. High volume builders may get better prices. Depending on these factors, it might cost $0.80 to $3.00 per square foot. Be sure to check with a local installer for pricing in your area.
Advantages
Aerobarrier offers advantages to every building project where air sealing is a priority. The system reduces headaches for builders and speeds construction. While gross sealing measures, such as fire caulking, large penetrations and hidden air barriers, are still required, the final responsibility is assigned to one subcontractor who can dial in a specific leakage rate in less than one day. In the past, air sealing activities would span virtually every stage of construction, but the result wouldn’t be known until the building was complete and corrections would then be difficult to make.
Consistency is a another benefit, especially for high-volume builders for whom an air tightness level of 3.0 ACH50 has become a common target for building science or for economic reasons. With Aerobarrier it’s easy to hit this target in every home. This consistency is valuable for designing appropriate ventilation systems, which should complement building leakage. The system works just as well with complex architecture as it does with simple designs. In either case, Aerobarrier takes the stress and uncertainty out of the air sealing process.
One additional advantage – depending on the project – is cost. If a builder’s current practice requires a few cases of caulk and a couple of days of labor, then their current practice may be less expensive than Aerobarrier, which may cost several thousand dollars to bring a typical home to a typical level of tightness. On the other hand, super air sealing at 2.0 ACH50 or below requires more time, materials, and supervision of multiple tradespeople. And often it requires additional sealing after the blower door test is run. Aerobarrier could well be less expensive than these more sophisticated options. Many builders use proprietary air sealing wraps, sheathing or fluid applications, which have their own costs. The final analysis will depend on the specific circumstances of the job.
Perhaps the biggest advantage to using Aerobarrier would be in existing homes where many leakage sites are simply inaccessible without major demolition. In this situation, Aerobarrier can achieve far greater levels of air tightness. The process here would be similar to spray painting the interior, involving moving furniture and masking windows, etc.
History
The idea behind Aerobarrier isn’t new. The concept, originally called Aeroseal, was developed in 1994 by Dr. Mark Modera at Lawrence Berkeley National Laboratory. HVAC contractors began using the Aeroseal system on heating and cooling ducts in the field in 1997. Over time, the concept was adapted to entire buildings and in late 2017, Aerobarrier was introduced at the International Builders Show.
Will Aerobarrier revolutionize building air sealing? If you have thoughts, please share them in the comments section below.
Mike Ardeljan says:
This is great, thank you! Overall very well done. We had a few little corrections or clarifications:
Under “How it Works”
The timeline is a big deal to the builders and a more accurate representation on the process on a typical residential home is closer to 1-2 hours of actual sealing time to hit the target and a total of 3-4 hours on site including preparation and clean up.
Under “Cost”
While the costs stated are fine and have been offered for advantageous “wholesale” pricing, we think the industry standard in an information article like this on any product is “retail” pricing, right? Retail pricing for us is $1.50 to $3.50/sf. It is totally fair to say volume discounts are available and there are a few cases were more prep might be needed and cot would be a little higher.
Under “Advantages”
The article states that ‘Aerobarrier could well be less expensive than these more sophisticated options.’ Having air sealed for years with several of the other options described and then with Aerobarrier, we believe the older options are hardly more sophisticated, quite the opposite, more cumbersome, time consuming, costly and uncertain, making them less sophisticated in both process and result. We propose that it would be fair and more accurate to use a descriptive word for the other options such as ‘complicated’ or ‘involved’. For example, ‘Aerobarrier could well be less expensive than these more complicated/involved options.’
Thanks again for this well crafted piece on Aerobarrier. We really appreciate it and are excited to get the word out to the building industry!
Bruce Sullivan says:
Mike,
Thanks for these thoughts and clarifications. As an Aerobarrier provider you can speak specifically to your situtation. It’s an amazing technology and I hope that it allows the industry to move toward tighter homes everytime and everywhere.
Bruce
Xuaco Pascual says:
Very interesting concept. Having seen many projects require iterative air sealing to achieve specs, this could simplify that process. Will research further
Johann Ohly says:
How well does the acrylic material resist shrinkage over time? Does it become brittle? Has the ACH50 test been repeated 1, 2, 3, + years after installation and what were the results?
Patrick Fritsch says:
I agree with your doubts, this AeroBarrier is essentially a caulking and we all know caulking has a certain lifespan especially if exposed to UV and/or heat, depending on the type acrylic caulking usually 5 to 10% shrinkage (depends on additives). Another suspicion of mine is that since they vapourize it through the air it’s probably diluted with a water/solvent substantially more than a regular caulking therefore may shrink even more over time. I guess it’s the same as for all innovative new products…only time will tell.
Bruce Sullivan says:
Johann,
These are good questions and we have asked our local Aerobarrier installer to provide information on durability. I doubt that UV will be an issue because the sealant is not exposed to direct sunlight. I do know that the acrylic sealant is the same basic material as the company has been using for a couple of decades in their Aeroseal duct sealing system. It would seem that they have a track record. We hope to have more information later this week. Please stay tuned.
Bruce
Peter Grube says:
As experienced high-performance home design/construction professionals committed to best building practices, we welcome vetting, due diligence and discussion around any new building technology or product.
As builders and designers, we have been engaging in assessing new building technologies and products for over a decade. Upon learning about AeroBarrier and the promise of aerosol air sealing we had the same legitimate questions about the technology we hear from you and others. And we carefully investigated this technology – confirming for ourselves that it performs as advertised in every respect before we became AeroBarrier vendors.
Our vetting included: a deep dive into the sealant durability (3rd party lab testing); health effects (GreenGuard Gold Certified); site visit and demonstrations with a multi-year, beta-tester builder (Mandalay Homes, Prescott, AZ) who has used AeroBarrier in hundreds of homes with several years of compelling follow up performance testing; and meeting the technology’s inventor (Mark Modera) and development team (Amit Gupta) behind the technology. The effectiveness, health, safety, durability, and ability to advance the building industry were all critically important to us. In every one of these categories we were impressed with the AeroBarrier technology and made the business decision to become vendors.
With this background, we welcome all questions about the AeroBarrier sealant and installation technology. We strive to help building professionals develop a factual understanding of the system.
In response to the concerns stated, AeroBarrier is not a “caulk’’. Caulks have a lifespan, especially when exposed to UV and/or heat, and usually shrink depending on additives. AeroBarrier X1, manufactured by Tremco, is a proprietary waterborne acrylic sealant. While in similar category of materials, the AeroBarrier X1 sealant is not a ‘regular caulk’, and is not ‘diluted.” It is a water borne acrylic sealant developed specifically for application as an aerosol mist. The fact is that AeroSeal, a company with decades long history in aerosol air sealing, and Tremco, the manufacturer of AeroBarrier X1 sealant, with a decades long history of sealant manufacturing, had rigorous independent 3rd party testing of the sealant completed before going to market. This testing (download) addressed flexing, aging (durability), sealing performance and compatibility.
This 3rd party testing concluded “simulating a fifty-year period of service, the sealant showed no evidence of cracking, crazing, or spalling. Furthermore, the sealing performance was 0.13% leakage (very low) when compared to open-joint condition (no sealant present). Finally, there was no discoloration and/or material breakdown at the sealant interface with the 41 common building products, indicating favorable compatibility.”
Please review the durability testing results in the link above to fill in details about the rigorous nature of the testing relative to flexing, aging, performance, and compatibility. The AeroBarrier X1 Product Data Sheet is also attached for additional information. After our independent vetting of AeroBarrier technology and the sealant itself, we are confident that we are providing the building industry with a superior option for simple, verified envelope sealing using a stable, non-toxic, flexible, durable sealant.
Ultimately, our goal is to enable builders to effectively improve their building envelope performance by overcoming the challenges commonly associated with older methods of air sealing. With AeroBarrier we are providing one extremely effective and valuable solution. What methods, products and testing are you using now to get your current air sealing results? Are you able to measure your results? If so, you are ahead of the game, congratulations, and keep up the great work! If not, maybe we can help you get tighter while improving the precision and consistency of your results. If you don’t know, maybe we can help provide you with a single-step quantum leap forward in your building envelope performance.
This guy says:
$0.80-$3.00/ft is a fairly huge range. At the lower end, it’s completely justifiable. At the upper end, you’re going to see far fewer people interested.
Bruce Sullivan says:
As I understand it, pricing is set by local installers who operate in exclusive territories. So the cost varies widely across the country. While less expensive is always better for customers, I think a careful analysis is in order. Air sealing remains an extremely effective way to reduce energy use, improve durability, and improve the performance of controlled ventilation systems. If you’re trying to reach 3.0 ACH50, then you do have less expensive options. If you’re trying to reach 1.0 ACH50, it takes more material and much more time. You should also weigh the impact of a couple of thousand dollars spent on air sealing with the cost of thick walls (greater than 6 inches) and even the number of solar panels you would need. Finally, the climate has a big impact. In warmer climates, very high levels of insulation may not make sense, but air sealing does. A good energy model can help you compare the benefits of various approaches with the costs. It all comes down to the aggregate cost of a package of features that bring you to your energy goal. For ZEP, that means zero energy or zero carbon. I think Aerobarrier holds enormous promise for achieving super-tight construction that is cost-effective, reliable, and predictable. I would love to hear from anyone that has experience with the system.
Alex Walters says:
Energy efficiency is one of the easiest and most cost-effective ways to combat climate change, clean the air we breathe, improve the competitiveness of our businesses and reduce energy costs for consumers.
Would you like to learn more? Green Training USA – http://www.greentrainingusa.com
Joe Emerson says:
We agree!