Stephen Aiguier, founder and CEO of Green Hammer talks with ZEP founder Joe Emerson. Aiguier is a well-respected leader in the movement for healthy, zero carbon buildings. In addition to guiding the team at Green Hammer, Aiguier teaches the Sustainable Homes Professional series each year in Portland, Oregon.
JE: Who is Green Hammer and what is your mission?
SA: Green Hammer is a full-service architecture and construction firm specializing in designing and building healthy and durable zero energy homes, commercial spaces, and communities. Our mission is to engage in our Unified Design Build process to create healthy and inspiring buildings for life.
JE: How many zero energy homes have you designed and/or built?
SA: Green Hammer has designed and completed construction on a variety of zero energy projects: six single family residences, a small office building for CAPACES Leadership Institute, the Cowhorn wine tasting room, and a seven-unit, multifamily age-in-place community called Ankeny Row. We are currently in the design or construction process for several other zero energy projects including three single family homes, one of which is a full renovation of a 1980s home, a 17-unit multifamily community, a 12-unit age-in-place multifamily community, and a childcare facility.
JE: Can you tell us more about your zero energy developments or multi-family projects?
SA: Yes. We completed the design and construction of Ankeny Row, a seven-unit, multifamily age-in-place community in 2015. The community is now independently owned by the six different unit owners, each with a percentage share of the commons which includes a community garden space, extra storage, a common unit with an additional kitchen, bath, and living space where the unit owners gather to visit, do yoga, and share some of their meals together. Ankeny Row has now produced more energy than they’ve consumed as an entire community for both of the first two years the community has been operational.
We are also now under construction on two more communities: Tillamook Row a 17-unit community and Rose Villa, a 12-unit senior living community. Each project has a slightly different ownership model and will be completed late fall of 2018 and early spring of 2019 respectively.
JE: What motivated you to begin designing and building zero energy homes?
SA: We established a mission to create healthy and inspiring buildings for life out of a love for our planet and a deep concern for the oversized footprint and negative impacts of human-built environments, We define “healthy” to mean our buildings must have clean interior air, eliminate materials that contain toxic ingredients as much as feasible, support a responsible supply chain, and establish a long-term, healthy relationship with the natural world. We define “inspiring” to mean beauty, innovation, and aspiration. We know every building must be beautiful or we risk wasting the precious natural resources we wish to preserve, and we must continue to push each of our buildings to always be healthier than the last and inspire others to follow our path. We finish our mission statement with “for life,” meaning both that we intend our buildings to span multiple generations and for them to have a positive relationship with the living world from concept through the multiple generations of occupancy.
A building’s operational energy use has the most significant negative impacts on climate change, and energy production at the grid level results in significant disbursement of toxics into the environment. By creating buildings that produce as much or more renewable energy than they consume from the grid we are making significant gains toward our goal in achieving healthy and inspiring buildings.
JE: What is unique about your Unified Design Build process?
SA: Most of the construction and architecture professionals in our industry are taught and practice the design-bid-build process where an owner would engage an architect initially to execute the design and then put that design out to bid to three or more contractors to build the project. There are inherent issues with this process, especially when trying to achieve higher standards in the work. The architect or designer is left to make all the decisions around how to best manage innovative details like air barriers and exterior insulation in the most constructable, cost effective means and the builder is expected to understand all of the intent of the design and project criteria without being a part of the initial decision-making and design process. The results are often ugly, where the budget drifts far out of reach and the construction morphs from the original intent in an effort to manage the changes. Frequently, the contractor and architect are left blaming each other for the issues. As a result, animosity between contractors and architects can run deep.
As we were building our design-build firm we kept bumping into issues around how to re-train our staff to trust each other and break from their years of training in the standard industry where trust between designers and builders had broken down. Initially a lot of our efforts were just working on our company team integrity values and discovering how we best work together. Ultimately, team values alone is not enough. We learned we needed a more specific way to integrate that was standardized across all of our projects. In seeking standardized processes for design build, we found the Integrated Design Process (IDP) and the Integrated Project Delivery (IPD) process.
Ultimately, both were tremendously helpful and also very generalized in their descriptions with the added advantage that the IPD came with contracts to facilitate collaborations between architecture and construction and do so in a way that further describes some expectations in working together. We discovered that for a small, integrated firm each process felt too general and were really meant to describe a method for separate design and build teams to work together, whereas we really wanted an internal process that worked to build off of our values and unique project goals. We also wanted a process that could scale from our commercial projects down to our residential renovations.
We decided to invest our own time and spent two years developing the first draft of our Unified Design Build Process (UDBP) manual and check sheets. We have since evolved that process in multiple revisions and updates. Our UDBP lays out the intent and the details necessary for each project team to intake a project and deliver it in a collaborative, unified, and organized manner that gives our project teams flexibility to make unique decisions while also laying out direct responsibility to each team member for all steps of designing and building a project. The UDBP has been a tremendous tool for onboarding new staff quickly into our project teams and ensuring they understand how we deliver our projects. We’ve seen fantastic results and consistent success with project management, client engagement, and project certifications delivered on time and on budget in a collaborative environment.
JE: What is the thing you like best about zero energy homes?
SA: The exceptionally happy client feedback is my favorite thing about zero energy homes. Even after we’ve explained to clients up front that living in a super-insulated, air-tight home with heat recovery ventilation will dramatically improve their living experience, we still always get calls and emails months later about how comfortable their home is and how the air always seems fresh and clean. It’s pretty awesome. My favorite thing is hearing about how kids who had previously struggled with chronic bronchitis or asthma experienced a tremendous drop or complete elimination of symptoms after moving into their zero energy home.
JE: What design details are most important to strong energy performance?
SA: Our building envelopes conserve far more energy than any of the solar photovoltaic panels produce on our buildings. A continuous air barrier on all six sides of the home, triple-pane windows and exterior doors, about 30-50% more insulation than a standard home, dramatic reductions on thermal bridging and 80% or better efficient heat recovery ventilation all make significant improvements to the energy performance of a home.
JE: What have you learned about designing and building zero energy homes so they are cost-effective and affordable?
SA: This is always a challenge as, fundamentally, zero energy homes require some extra steps and attention to detail around the air barrier and extra insulation that a standard home would not include. All other things being equal, the initial purchase cost will inherently be higher. “Affordable” and “cost effective” are interesting terms in the real estate market.
Banks see buildings as “cost effective” or “affordable” if they have a low cost per square foot (sf), which drives up square footage of housing. For instance a 4,000 sf house costs less per square foot to build than an 800 sf house as they both have similar overhead costs such as 1 sewer main, 1 new home permit (very seldom are permit costs based on sf), 1 water main, 1 power main, 1 driveway, etc., but the large home can spread those costs out across more sf thus driving down its cost per square foot. Larger homes also offer the builder the ability to negotiate better on volume discounts that would not be afforded to smaller projects. This is why the average starter new home is usually 2,000 sf or more. They appraise well on a lower cost per square foot basis and banks will finance them.
However, the best way to save on overall cost is to build small. Building small is a strategy we use for clients, but one that can be challenging with traditional financing. In these cases we will ask for an Accredited Green Appraiser who has been trained to recognize the additional value of zero energy homes and, eventually, we get the deal done. We also see multifamily buildings like row housing or apartments, as opportunities to build small and still benefit from the economies of scale of a larger project, which also helps make the homes more affordable for buyers.
Affordable has also been confused with the need to build as cheaply as possible, which is a real issue, especially for low-income home buyers. That is because by building cheaply you are inherently building with the lowest quality materials, especially for the roof and windows – fundamental features to the home’s long-term durability and, when done poorly, are susceptible to failure before the mortgage is paid off, often requiring a new mortgage to be taken on the home to pay for those replacement or repair costs. This creates a debt cycle that makes retirement or other long-term savings impossible for low-income home buyers. Our take on it is that the best gift of affordability is long term durability, which also adds some up front cost, but is most affordable for the buyer in the long run.
JE: Any more tips about how to keep costs down?
SA: Besides increasing the economy of scale with multifamily, the other trick we’ve learned is to keep it as simple and standard as feasible. When you have added details like air barriers and ventilation systems the building process is complicated enough. There is no need to try and reinvent “cost effective” building with new ways of doing things. What we’ve learned is that new and innovative usually, but not always, just adds tremendous costs as it’s new to everyone, so everyone charges a bit more, even if the new process turns out to be simple.
The zero energy home should, as much as feasible, be built with traditional building details. This allows trade partners to do what they know best, so they can focus on minimal new high-performance elements, and not just feel like they’ve been hired to build some experimental space ship they need to charge double for. I am pretty sure over the past 15 years we’ve built most types of wall systems seen in high performance housing from double walls, ICF, SIPs, to Larsen trusses, etc. What we build now looks much like a standard code home with a little exterior mineral wool or cork insulation. Let the large, well-financed, commercial projects experiment with new innovative construction technology. There’s no need to reinvent the wheel one house at a time.
Keep it simple and standard, then repeat.
JE: Are there any new technologies for reaching zero energy cost effectively that you are excited about?
SA: The cost of durable triple-pane windows with sub 0.18 U-values has dropped dramatically over the past four years with the advent of high-performance windows to the US market, primarily from Germany. There are now a few companies manufacturing these windows in the US and some larger domestic companies like VPI are starting to create their own lines, which will help improve the supply and lead times locally. Air barrier tapes and airtight weather resistant barrier systems are becoming more common and the amount of vapor-open, airtight, liquid-applied membranes available locally has dramatically increased as well, which is fundamentally changing the market. As more of these products are used commercially and more trade partners pick up the skills to install them, the costs will become more normalized to industry standards and performance will increase dramatically.
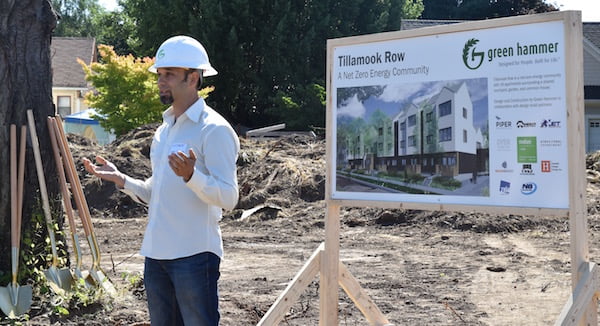
Stephen Aiguier, CEO and founder of Green Hammer, speaks at the groundbreaking ceremony for Tillamook Row, a zero energy multifamily project in Portland, Oregon.
JE: How would you advise designers and builders to reduce construction costs?
SA: Start the conversation on Day One and work together through the design and the build to make sure the details stay as simple and standard as feasible and the intent of the design and performance standards are met through to the finish line. I would also highly recommend using Earth Advantage as a zero energy standard to certify to. One huge advantage is that Earth Advantage will supply a building outreach specialist from the outsetto work with the team. The fee to get a full home certified to net zero is about $1,600, but the outreach specialist will handle all of the energy modeling and let you know if you are on track They’ll also submit all the necessary forms for the builder to get up to a $4,600 cash incentive from Energy Trust of Oregon for building a zero energy home. (Editor’s Note: There are energy performance professionals, also called raters, in most locations in North America to assist builders in a similar manner.) The benefits are huge and having an outreach specialist who has experience with multiple zero energy projects on the team is priceless, especially when working through all the details about how to get the project done cost effectively.
JE: What advice would you give a client beginning the process of looking for and buying a zero energy home?
SA: Have patience. There are very few zero energy homes currently on the market. Hopefully we meet governor Brown’s mandate to build to zero energy ready by 2023 and then this type of construction will be standard. Most importantly, look for a zero energy certification from Earth Advantage or the International Living Future Institute that the home can meet zero energy performance. Otherwise it’s like buying a fuel-efficient car that will not report its MPG rating. You have no idea if it will perform like a zero energy home should. Alternatively, hire a firm to design and build one for you. (I can think of one excellent option.)
JE: Do you have any advice to builders and designers who are not yet involved in zero energy home projects?
SA: From a performance standard, a zero energy style envelope is essentially the current code throughout Europe. And zero energy “ready” will be code in California starting in 2020 and is planned for the Oregon code by 2023. (“Ready” means it can meet zero energy standards if solar panels are added to the south face of the roof, or if sun were able to shine on the south face of the roof for shaded sites). If you are in the design or building industry for homes in Oregon, you have an excellent opportunity to get ahead of the market now. By incorporating zero energy ideas into your upcoming projects, you can deliver a better-than-average product while taking advantage of financial incentives and technical assistance. Or, you can kick and scream and be left in the dust.
JE: What was your experience with the financing and appraisal processes of zero energy homes you have sold? Do you have any suggestions for other builders?
SA: Builders will want assistance from Earth Advantage for the certification process and ask for Earth Advantage certified real estate agents and appraisers to help through the marketing and sale of the home. Do not over value the attractiveness of zero energy homes, it’s a nascent market and consumers don’t quite understand the value yet. Some studies show 4%-9% higher sale values for zero energy homes and I would still not venture far beyond that premium unless you have committed purchasers up front. A zero energy home can be built for less than a 10% cost premium if done effectively.
JE: Did you receive a third-party certification? If so, how important was that in your process?
SA: Yes, Green Hammer homes are Earth Advantage Platinum and Zero Energy Ready or Zero Energy certified. The certifications are critical to ensure the project team understands the project goal and with the Earth Advantage certifications we had the added bonus of a third party checking on our calculations and assumptions and, with multiple project teams, it offers peace of mind to know that we have that double check from an outside party.
JE: Do you live in a zero energy home? What do you like about it?
SA: I live in a 1922 bungalow on the National Historic Registry that I retrofitted. I am not allowed to have solar panels, so zero energy was out of the question and I was limited in how much I could impact the exterior of the home as well. I added about 1,000 sf of space by capturing living area in the basement and adding a small addition, more than doubling the previous square footage. Despite the added space, I cut the energy use of my home by 50%. In the end, my house was certified to Earth Advantage Platinum. Ultimately, my favorite upgrades are the airtight envelope (the house tested out at 1.5 ACH50 –pretty good for a 1922-built home) and my Zehnder heat recovery ventilation system. I have lived with bouts of asthma most of my life and I’ve never felt better since I renovated our home.
JE: What policies are needed to advance the movement toward zero energy building as standard practice in the construction industry?SA: Certainly step one is to establish airtightness and heat recovery ventilation requirements in building code for new homes. As soon as that happens, the entire market can start practicing the two most important steps of creating a zero energy home: increase the overall insulation requirements for the building envelope and start with U-0.20, or lower windows. This will drive the local window manufacturers already producing at this level, or close to it, into overdrive and will then finish off with driving down the overall u-value of the home. Then voilà! We’re there! Otherwise keep in touch with Earth Advantage, the Zero Energy Project, the Net Zero Energy Coalition and the variety of passive house groups like Passive House Northwest and learn about how to best engage in upcoming legislative opportunities.