Sandifer watches as a crane guides one of BrightBuilt Home’s latest zero energy homes onto its foundation — a powerful symbol of the approach his company takes. While the crane may be the most dramatic element of this approach, it’s just one of the many tools that make factory-built homes the future of residential zero energy construction.
Most construction industry professionals would agree that the way the U.S. builds homes is extremely slow to change. This leads to processes that are outdated, archaic, and inefficient. Site-built homes require dozens of workers from a wide array of trades. This hodgepodge leads to communication issues, lower quality construction, waste of building materials and time, conflicts, and unnecessary costs. Production builders hope to address these shortcomings by working with various levels of standardization. Nevertheless, issues remain such as weather, material quality, supply chains, small quantity pricing, and the thousands of miles workers travel to reach each site and return to their homes over the course of building each home.
Factory-built homes eliminate or at least simplify many of these issues by moving construction indoors, where the weather is always better, the materials are dry and secure, and standardization is easier to manage. This approach is clearly more successful in meeting the quality standards for getting to zero.
When BrightBuilt Home began operation in 2010, they had all the advantages of factory construction in mind. They also had another goal: to build each home to the highest standard of energy efficiency. Every home that leaves their factory is a zero energy ready home and buyers know exactly how much solar electric capacity would be required to reach full zero energy status. About 70% of clients add the solar panels needed. Sandifer, BrightBuilt Home’s director of sales, says that many of the remaining customers are so impressed with the low energy bills that they decide to hold off on solar for the time being.
Most of BrightBuilt’s homes are manufactured in partner factories in Maine or Pennsylvania for customers in New England. In this cooler climate, reaching zero means R-40 double-wall construction, R-60 ceilings, and window heat loss from U-0.14 to U-0.19. Most homes have air leakage rates below 1.0 air changes per hour at 50 Pascals, so they use energy recovery ventilation systems to maintain healthy indoor air. The homes’ cold climate mini-split heat pumps not only save precious indoor space, but handle Maine winters without issue.
A third partner factory in Pennsylvania manufactures homes with the same performance criteria, though homes in more southerly climes will have greater cooling loads and smaller heating loads. The science remains the same. The more the outside extremes are buffered, the easier it is to regulate the interior conditions.
After completion, modules up to 16 x 64 are loaded onto flatbed carriers and transported to the site where the crane sets them on a waiting foundation. The overwhelming advantage of modular construction is the speed of this final step. Most homes are weathertight within hours of arriving at the site.
Another advantage of factory construction is the high level of design certainty compared to most site-built homes. Every detail is nailed down before construction starts. And after the plans are final, shop drawings precisely define every detail. Change orders are strongly discouraged and often impossible. “This level of detail at the front end means few, if any, issues on the back end,” Sandifer said. “It also means a significant reduction in scope creep, keeping project budgets in check.”
BrightBuilt’s largest design offers 2,700 square feet (sf) of living space and arrives in four modules.
On the other end of the size spectrum is the new Sidekick line that requires only a single module, with living space ranging from around 400 to 800 sf. This line taps into a growing interest in very small homes, accessory dwelling units, and backyard studios.
“No two BrightBuilt homes are the same,” said Sandifer. The customer begins the process by choosing one of nine designs within the BrightBuilt core collection and they customize from there. Each site is analyzed for solar access and passive solar gain, and the design is adapted to these conditions, as well as specific client design and lifestyle requirements.
Sandifer explains that it takes very little convincing for customers to accept the zero energy ready feature package. “Before they come to us, they already know the benefits of zero energy homes. That’s why they searched us out,” said Sandifer. “They want to tread more lightly.”
“Our zero energy homes are attainable because the owner sees a lower overall monthly cost,” he added. Here is the standard cost comparison.
With lower monthly energy costs, you invest an additional $35,000 to $50,000 in your home instead of giving it away to the utility company.
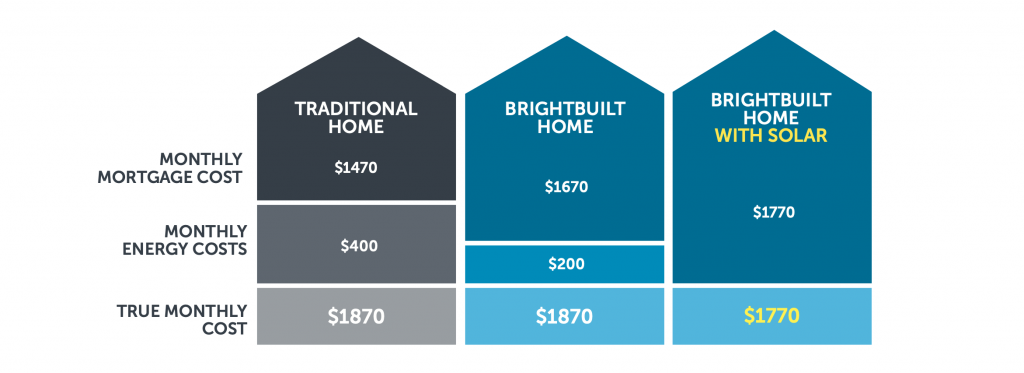
This illustration is based on a 1750 square foot home with a 30 year mortgage at 4% interest. It’s approximately 12% more initial cost for BrighBuilt above a traditional house and assumes typical energy costs for a family of four, residing in New England. The package includes a 10 kiloWatt solar array at $2/watt with incentives.
BrightBuilt offers a free e-book describing their process, which serves as an excellent primer on zero energy design. In the past year, BrightBuilt had shipped homes all over the Northeast and Mid-Atlantic, and they believe their homes are attainable no matter where you live.
Like almost everyone in the zero energy home movement, Sandifer noted how high-performance homes could have weathered the polar vortex and the resulting Texas grid failure. More insulation, tighter construction, and efficient mechanical equipment would have put far less strain on the utility infrastructure and would have reduced the pain of a long-term power outage.
“If all homes were built to the zero energy ready standard, they would be less taxing on the system and less devastating for families,” he said.
What’s next for BrightBuilt Homes? Sandifer says they have been looking into solar roofing materials, such as the Tesla Solar Roof. It seems like an appropriate move for a forward-thinking homebuilder.