We are proud to feature one of our valued sponsors.
Starting with SIP panels saves money through easier, speedy construction, decreased labor on-site, and reduced use of raw materials. Meanwhile, the high-performance building envelopes that insulated panels provide can realize healthier, more comfortable, resilient, and sustainable homes with improved indoor air quality (IAQ) and utility savings of 50 percent or more. These long-term savings make panelized-construction homes a consistently low-cost alternative to traditional stick-built framing.
What is SIP construction?
SIPs are high-performance, insulated panels for framing residential and light commercial buildings. Each prefabricated panel consists of an insulating foam core, sandwiched between two structural facings, typically oriented strand board (OSB). Because SIPs are manufactured under factory-controlled conditions, they can be fabricated precisely to fit nearly any design. The results are strong, energy-efficient, and cost-effective buildings.
Speed and simplicity
SIP panels cost vs stick-built
Panelized construction may seem more expensive up front, but SIPs offer savings over stick-built due to decreased construction and labor costs. Prefabricated wall and roof assemblies install in sections (with a lift truck and construction crane), and framing crews pick up installation techniques quickly. Openings and chases are precut at the factory, which makes the plumbing and electrical work go smoothly. SIPs provide a uniform nailing surface to quickly attach siding and trim. And since the insulation is part of the system, you get higher performance with less on-site work.
Research has shown 55% to 66% savings in labor-hours in framing residential construction, including midrise multifamily housing. This translates to comparably faster on-site construction overall. Over the past 30 years, members of the Structural Insulated Panel Association (SIPA) (private and public organizations including the US Department of Energy, state energy efficiency programs, and national nonprofits like Habitat for Humanity) have collaborated to research and advance quality, energy-efficient construction with SIP panels. The website offers a trove of documentation, design guides, educational programs, and fact sheets to share with builders and homeowners. For architects, online education modules offer up to 7.5 hours of AIA accredited HSW courses.
SIP panels cost comparison tool
Volatile prices for lumber, labor, and jobsite waste removal all add cost and delays to your projects. SIPA’s Project Profiles demonstrate that panelized construction costs less when these factors are considered. The calculator tool at SIPsTrueCost.org helps builders and owners make informed decisions about what SIP panels cost for their own, specific project parameters; they can even use prepared bids (conventional) to compare cost savings of SIPs versus conventional framing.
SIP panels are tough!
Insulated panels are the resilient choice. They have been used in high-wind designs (in excess of 180 mph) and are approved for Florida’s strict High Velocity Hurricane Zones (HVHZ). And panelized construction can be used in all seismic design categories. Testing indicates that SIPs will stand up to moisture, even flooding water, during construction with no significant loss in transverse, lateral, or axial strength. SIPA members provide individual, third-party recognition of compliance with the International Building Code (IBC) and International Residential Code (IRC) through evaluation reports, typically issued by ICC-ES. The SIPA Master Code Report code listing is shared by a group of SIPA member manufacturers.
Energy efficiency is where insulated panels shine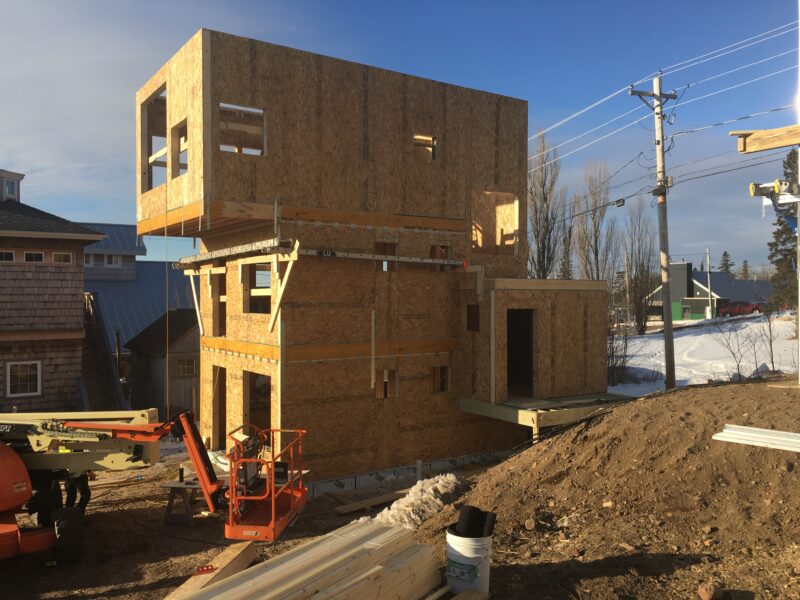
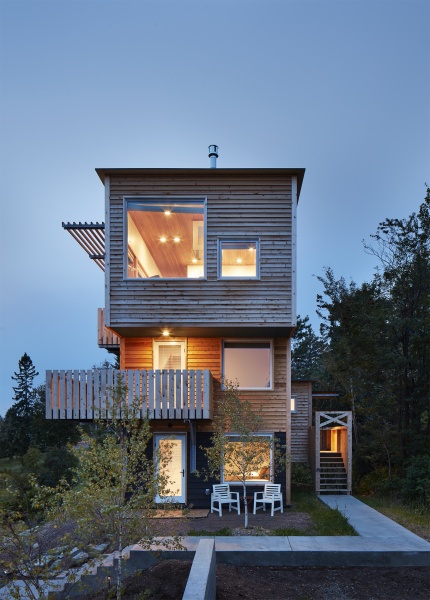
Building with SIP panels creates a superior building envelope with excellent thermal resistance and minimal air infiltration. Oak Ridge National Laboratory research on whole-wall R-value shows that a 4-inch SIP wall rated at R-14 outperforms a 2X6 stick-framed wall with R-19 fiberglass insulation. Insulated panels’ high R-values are reinforced by very low thermal bridging. Factory precision ensures tight construction.
Up to 40% of a home’s heat loss is due to air leakage, so tighter homes use less energy, reducing climate change from burning fossil fuels. Consequently, HVAC systems needn’t work so hard. Mechanical systems can be sized smaller (less-expensive) and more energy-efficient. Plus the equipment and ductwork reside within conditioned spaces, resulting in major energy savings over time.
And insulated panels use resources efficiently while minimizing pollution that can harm the environment. An EPS insulating core is typically used. This is made from petroleum products, which is less desirable sourcing than renewable resources, however it uses 24% less energy to produce than fiberglass insulation of equivalent R-value. SIPs’ embodied energy payback is typically after 3 to 5 years of in service. The carbon from their petroleum ingredients is locked in or sequestered (much in the same way wood holds carbon in cellulose).
The OSB facings are manufactured from fast-growing, renewable wood resources. Centralized manufacturing wastes less material, and leaves far less waste on the construction jobsite that needs to be hauled away and recycled or landfilled. Any reputable SIPs manufacturer will promote third-party life-cycle studies and thorough environmental product declarations.
But reducing energy consumed for heating and cooling, year after year over the course of a home’s 30 to 50, perhaps 100 year life, produces the most substantial contribution to fighting climate change and protecting the environment. Comparative lifecycle analyses point to reliable energy saving and reduced greenhouse gas emissions. Panelized construction is the optimal way to achieve a HERS rating well below the national average. And SIP panels are so reliable that Energy Star no longer requires a blower door test for SIP homes to earn Energy Star approval.
Certifications with creative panelized construction
Few building systems address budget, environmental, resource management, and comfort concerns in a single package. Because they are engineered for strength, insulated panels allow for open floor plans, architectural creativity, and aesthetic appeal to please both professionals and homeowners. While less than 2% of homes being built today use panelized construction, SIP panels are the starting point for hundreds of LEED Certified, Zero Energy Ready, Passive House, and Energy Star homes. The 2022 Inflation Reduction Act (IRA) brings a fresh wave of tax credits for energy-efficient homes and extends the terms for claiming existing credits. Sustainable panelized construction will likely boom as the cost of SIP panels continues to come down, blazing a path for homebuilders to reap the benefits of IRA tax credits.
Healthy homes for a healthy planet
A building envelope is the armor that protects inhabitants, as well as interior finishes, furnishings and equipment. In the walls, roof, flooring, healthy materials are important to anyone suffering respiratory problems, like allergies and asthma. A well-designed home envelope is durable, healthy, insulating, and tightly sealed. Panelized construction homes are engineered to bring these qualities together.
In a well-sealed building, fresh air is provided through controlled ventilation systems, ensuring occupants breathe healthier, filtered air, and removing pollutants produced inside the home (dust, CO2, natural gas byproducts, etc.). Heating and cooling are maintained more efficiently and more comfortably, without leaking conditioned air through gaps in doors, walls, and ceilings. This means no drafts or ingress of polluted air, particularly during pollen or smoke advisories! SIPs have uniform insulation, which means there are no cavities where moisture might accumulate and promote mold, mildew, or rot.
Where you’re stopping air leaks you’re also blocking noise transmission pathways, leading to a quieter, and perhaps more private, living situation.
The components in insulated panels (including adhesives) meet some of the most stringent standards for indoor air quality, with low off-gassing. SIP panels have such low formaldehyde emission levels that they easily meet or are exempt from US Housing and Urban Development and California Air Resources Board (CARB) standards.
Building toward zero
If you are targeting zero energy or zero operating carbon, choosing panelized construction is a great first step. SIPs win several Department of Energy Zero Energy Housing Awards each year for low energy and zero energy. And the SIPA site features an online projects map with more than 800 searchable case studies of net zero and net zero–ready buildings.
From cradle to grave, lifecycle analyses demonstrate that, over the course of 50 years, the average energy saved is almost 10 times the extra energy invested when using SIPs, compared to traditional stick built. This represents an energy payback period of 5.1 years and a recapture of embodied greenhouse gas emissions in 3.8 years for American homes. In Canada, the analysis shows a return on energy invested in 2.7 years and greenhouse gas emissions in 2.7 years. An excellent return on investment by any measure.
Get inspired by SIPA’s Building Excellence Award Winners and then find out what SIP panels cost for your project
Our team researches products, companies, studies, and techniques to bring you the best of zero building. Zero Energy Project does not independently verify the accuracy of all claims regarding featured products, manufacturers, or linked articles. Additionally, product and brand mentions on Zero Energy Project do not imply endorsement or sponsorship unless specified otherwise.
Raj says:
Hi
I can read topic for SIP panels zero energy. Very nice usefull & helpful details.